Excavation and trenching are among the most hazardous construction operations. Cave-ins pose the greatest risk and are much more likely than other excavation-related accidents to result in worker fatalities. Employers must ensure that workers enter trenches only after adequate protections are in place to address cave-in hazards.
Other potential hazards include falls, falling loads, hazardous atmospheres, and incidents involving mobile equipment.
Scope
The Occupational Safety and Health Administration (OSHA) excavation standard applies to all open excavations made in the Earth’s surface. Excavations are defined to include trenches.
This standard is found at 29 CFR Subpart P and Appendices A through F — Excavations.
The standard does not apply to house foundation/basement excavations, including those that become trenches by definition when constructing formwork, foundations, or walls. This exemption does not apply to utility excavations or trenches, which are covered by 1926.652.
Definitions
- Terms associated with excavation operations can enhance understanding and simplify planning when these terms are properly defined.
Cave-in: The separation of a mass of soil or rock material from the side of an excavation, or the loss of soil from under a trench shield or support system, and its sudden movement into the excavation, either by falling or sliding, in sufficient quantity so it could entrap, bury, or otherwise injure and immobilize a person.
Competent person: One who is capable of identifying existing and predictable hazards in the surroundings, or working conditions that are unsanitary, hazardous, or dangerous to employees, and who has authorization to take prompt corrective measures to eliminate them.
Excavation: Any man-made cut, cavity, trench, or depression in an earth surface, formed by earth removal.
Protective system: A method of protecting employees from cave-ins, from material that could fall or roll from an excavation face or into an excavation, or from the collapse of adjacent structures. Protective systems include support systems, sloping and benching systems, shield systems, and other systems that provide the necessary protection.
Shield (Shield system): A structure that is able to withstand the forces imposed on it by a cave-in and thereby protect employees within the structure. Shields can be permanent structures or can be designed to be portable and moved along as work progresses. Additionally, shields can be either premanufactured or job-built in accordance with 1926.652(c)(3) or (c)(4). Shields used in trenches are usually referred to as “trench boxes” or “trench shields.”
Shoring (Shoring system): A structure such as a metal hydraulic, mechanical, or timber shoring system that supports the sides of an excavation and which is designed to prevent cave-ins.
Sloping (Sloping system): A method of protecting employees from cave-ins by excavating to form sides of an excavation that are inclined away from the excavation so as to prevent cave-ins. The angle of incline required to prevent a cave-in varies with differences in such factors as the soil type, environmental conditions of exposure, and application of surcharge loads.
Soil types:
- Stable Rock — Natural solid mineral matter that can be excavated with vertical sides and remain intact while exposed.
- Type A — Cohesive soils with an unconfined compressive strength of 1.5 tons per square foot (tsf) (144 kPa) or greater. Examples include: clay, silty clay, sandy clay, and clay loam. Certain conditions preclude soil from being classified as Type A. For example, no soil is Type A if it is fissured or has been previously disturbed.
- Type B — Includes cohesive soil with an unconfined compressive strength greater than 0.5 tsf (48 kPa) but less than 1.5 tsf (144 kPa) and granular cohesionless soils (such as angular gravel, similar to crushed rock, silt, silt loam, sandy loam, and, in some cases, silty clay loam and sandy clay loam).
- Type C — Cohesive soil with an unconfined compressive strength of 0.5 tsf (48 kPa) or less, granular soils (including gravel, sand, and loamy sand), submerged soil or soil from which water is freely seeping, submerged rock that is not stable, or material in a sloped, layered system where the layers dip into the excavation or with a slope of four horizontal to one vertical (4H:1V) or steeper.
Note: Unconfined compressive strength means the load per unit area at which a soil will fail in compression. It can be determined by laboratory testing or estimated in the field using a pocket penetrometer, thumb penetration tests, or other methods.
Trench (Trench excavation): A narrow excavation (in relation to its length) made below the surface of the ground. In general, the depth is greater than the width, but the width of a trench (measured at the bottom) is not greater than 15 feet (4.6 m). If forms or other structures are installed or constructed in an excavation so as to reduce the dimension measured from the forms or structure to the side of the excavation to 15 feet (4.6 m) or less (measured at the bottom of the excavation), the excavation is also considered to be a trench.
Preplan the excavation work
- Learning as much as possible about a jobsite before preparing a bid and having OSHA-compliant materials on hand contribute to successful excavation operations.
- Employers should share the details of safety and health programs with employees and stress how crucial it is for workers to keep the jobsite safe.
No matter how many trenching, shoring, and backfilling jobs one has done in the past, it’s important to approach each new job with the utmost care and preparation. Many on-the-job accidents result directly from inadequate initial planning. Waiting until after the work has started to correct mistakes in shoring or sloping slows down the operation, adds to the cost, and increases the possibility of a cave-in or other excavation failure.
Consider safety factors when bidding on a job
Before preparing a bid, an employer should know as much as possible about the jobsite and the materials necessary to perform work safely and in compliance with Occupational Safety and Health Administration (OSHA) standards. A safety checklist may prove helpful when considering specific site conditions such as:
- Traffic,
- Proximity and physical conditions of nearby structures,
- Soil,
- Surface and groundwater,
- Location of the water table,
- Overhead and underground utilities, and
- Weather.
These and other conditions can be determined through jobsite studies, observations, test borings for soil type or conditions, and consultations with local officials and utility companies. This information will help to determine the amount, kind, and cost of safety equipment needed to perform the work in the safest manner possible.
Avoid hitting underground utility lines and pipes
Before starting work, the OSHA standard requires employers planning an excavation to:
- Determine the approximate location of utility installations — sewer, telephone, fuel, electric, and water lines, or any other underground installations.
- Contact the utility companies or owners involved to inform them of the proposed work within established or customary local response times.
- Ask the utility companies or owners to find the exact location of underground installations. If they cannot respond within 24 hours (unless the period required by state or local law is longer) or cannot find the exact location of the utility installations, the excavation may proceed with caution.
If excavation work exposes underground installations, OSHA regulations require these installations to be protected, properly supported, or removed.
Communicate with workers before project starts
Share safety and health program details with employees and stress the critical role expected of them to keep the jobsite safe. Emphasize specific rules to help reduce the risk of on-the-job injuries. These rules may include requirements that workers:
- Remove or minimize all surface obstacles at the worksite that may create a hazard,
- Wear employer-provided warning vests or other reflective or high-visibility garments when they are exposed to vehicular traffic,
- Wear or use prescribed protective gear and equipment correctly,
- Operate equipment only if they have been trained properly in its use and alerted to its potential hazards, and
- Follow safe work practices.
It also is important to establish and maintain a safety and health management system for the worksite that provides adequate systematic policies, procedures, and practices to protect employees from, and allow them to recognize, job-related safety and health hazards.
Role of the competent person
- A variety of duties are performed by the designated competent person, including inspections, soil classification, and monitoring equipment.
- Soil is classified into four main groups: Stable Rock, Type A, Type B, and Type C. These categories are based on order of stability.
A competent person is an individual, designated by the employer, who can identify existing and predictable hazards in the surroundings or working conditions that are unsanitary, hazardous, or dangerous to workers, and who is authorized to take prompt corrective measures to eliminate them.
Tasks performed by the competent person include:
- Conducting inspections
- Classifying soil
- Inspecting protective systems
- Designing structural ramps
- Monitoring water removal equipment
Conduct inspections
Make sure the competent person conducts daily inspections of excavations, adjacent areas, and protective systems for evidence of a situation that could result in possible cave-ins, indications of failure of protective systems, hazardous atmospheres, or other hazardous conditions. Perform an inspection prior to the start of work and as needed throughout the shift. Make sure inspections occur after every rainstorm or other hazard-increasing occurrence. These inspections are only required when employee exposure can be reasonably anticipated.
Classify the soil
The soil classification system is a method of categorizing soil and rock deposits in a hierarchy of Stable Rock, Type A, Type B, and Type C, in decreasing order of stability. Categories are determined based on an analysis of properties and performance characteristics of the deposits and environmental conditions of exposure.
The competent person performs soil classification that is needed when:
- A sloping or benching system is designed as a method of protection for employees from cave-ins;
- Timber shoring for excavations is designed as a method of protection from cave-ins;
- Aluminum hydraulic shoring is designed; and
- Other protective systems are designed and selected for use from data prepared, and the use of data is predicated on the use of the soil classification system defined in a separate section.
Classification of the deposits is made based on the results of at least one visual and at least one manual analysis.
Visual analysis is conducted to determine qualitative information regarding the excavation site in general, the soil adjacent to the excavation, the soil forming the sides of the open excavation, and the soil taken as samples from excavated material.
Manual analysis of soil samples is conducted to determine quantitative as well as qualitative properties of soil and to provide more information to classify soil properly.
If, after classifying a deposit, the properties, factors, or conditions affecting its classification change in any way, the competent person must evaluate those changes. The deposit is reclassified as necessary to reflect the changed circumstances.
Inspect protective systems
The competent person must inspect an employer’s protective systems for any sign of damaged materials and equipment. Unsafe materials and equipment should be removed from service until a registered professional engineer evaluates and approves them for use.
Design protective systems
Any structural ramps used in an operation must be designed by a competent person if they are used for employee access or egress, or by a competent person qualified in structural design if they are used for vehicles.
Monitor water removal equipment
If water removal equipment is used to control or prevent water accumulation, an employer must ensure that a competent person monitors the equipment and its operation to ensure proper use. In addition, a competent person must inspect excavations subject to runoffs from heavy rains.
Use protective systems
- OSHA mandates that all excavations that come with the risk of cave-ins be protected by a system such as sloping or benching, or the use of shielding.
- Tables and charts approved by a registered professional engineer can facilitate the process of designing an excavation.
When done safely, trenching operations can reduce worker exposure to cave-ins, falling loads, hazardous atmospheres, and hazards from mobile equipment.
One of the most important ways to ensure workers in excavations are safe is to use protective systems, which are designed to protect workers by preventing trench walls from collapsing.
Prevent cave-ins
The Occupational Safety and Health Administration (OSHA) requires that all excavations in which employees could potentially be exposed to cave-ins be protected by one of the following methods:
- Sloping or benching the sides of the excavation, or
- Supporting the sides of the excavation by placing a shield between the side of the excavation and the work area.
Choose appropriate protective system design
Designing a protective system can be complex because many factors must be considered: soil classification, depth of cut, water content of soil, changes due to weather and climate, or other operations in the vicinity. An employer is free to choose the most practical design approach for any particular circumstance. Once an approach is selected, however, the system must meet the required performance criteria.
The OSHA standard describes methods and approaches for designing protective systems such as the following:
- Sloping/Benching
Sloping consists of forming sides of an excavation that are inclined away from the excavation. Slope the sides to an angle not steeper than 1½ to 1; for example, for every foot of depth, the trench must be excavated back 1½ feet. All simple slope excavations 20 feet or less deep should have a maximum allowable slope of 1½ to 1. These slopes must be excavated to form configurations similar to those for Type C soil, as described in Appendix B of the standard. A slope of this gradation or less is safe for any type of soil.
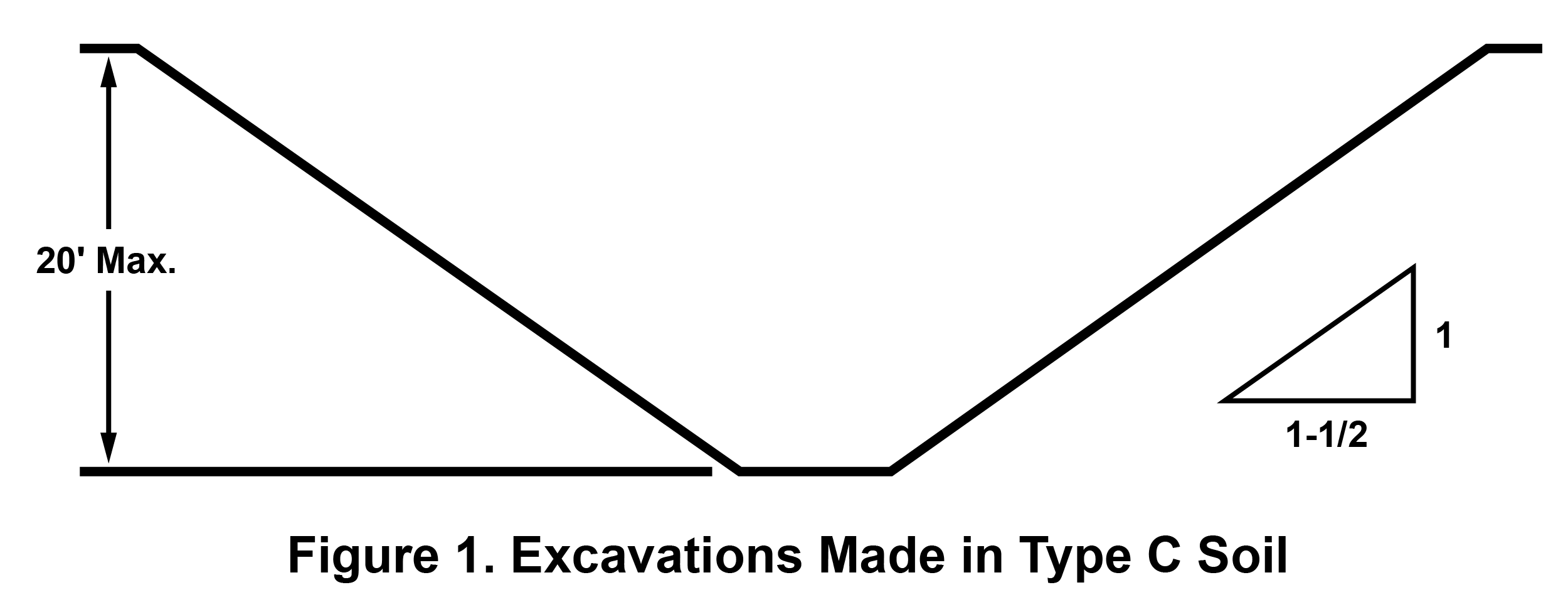
Benching is similar to sloping but involves further excavating the sides of an excavation to form one or a series of horizontal levels or steps. - Shielding/Trench box
Shielding can be permanent or portable, and it is also known as a trench box or trench shield. Shoring supports the sides of the trench and is often a metal hydraulic, mechanical, or timber shoring system.
Use a trench box or shield designed or approved by a registered professional engineer or based on tabulated data prepared or approved by a registered professional engineer. Timber, aluminum, or other suitable materials may also be used. OSHA standards permit the use of a trench shield (also known as a welder’s hut) if it provides at least the same level of protection as the appropriate shoring system.
Employers can choose the most practical method for the particular circumstance, but that system must meet the required performance criteria. The standard does not require a protective system when an excavation is made entirely in stable rock or is less than five feet deep, if a competent person has examined the ground and found no indication of a potential cave-in.
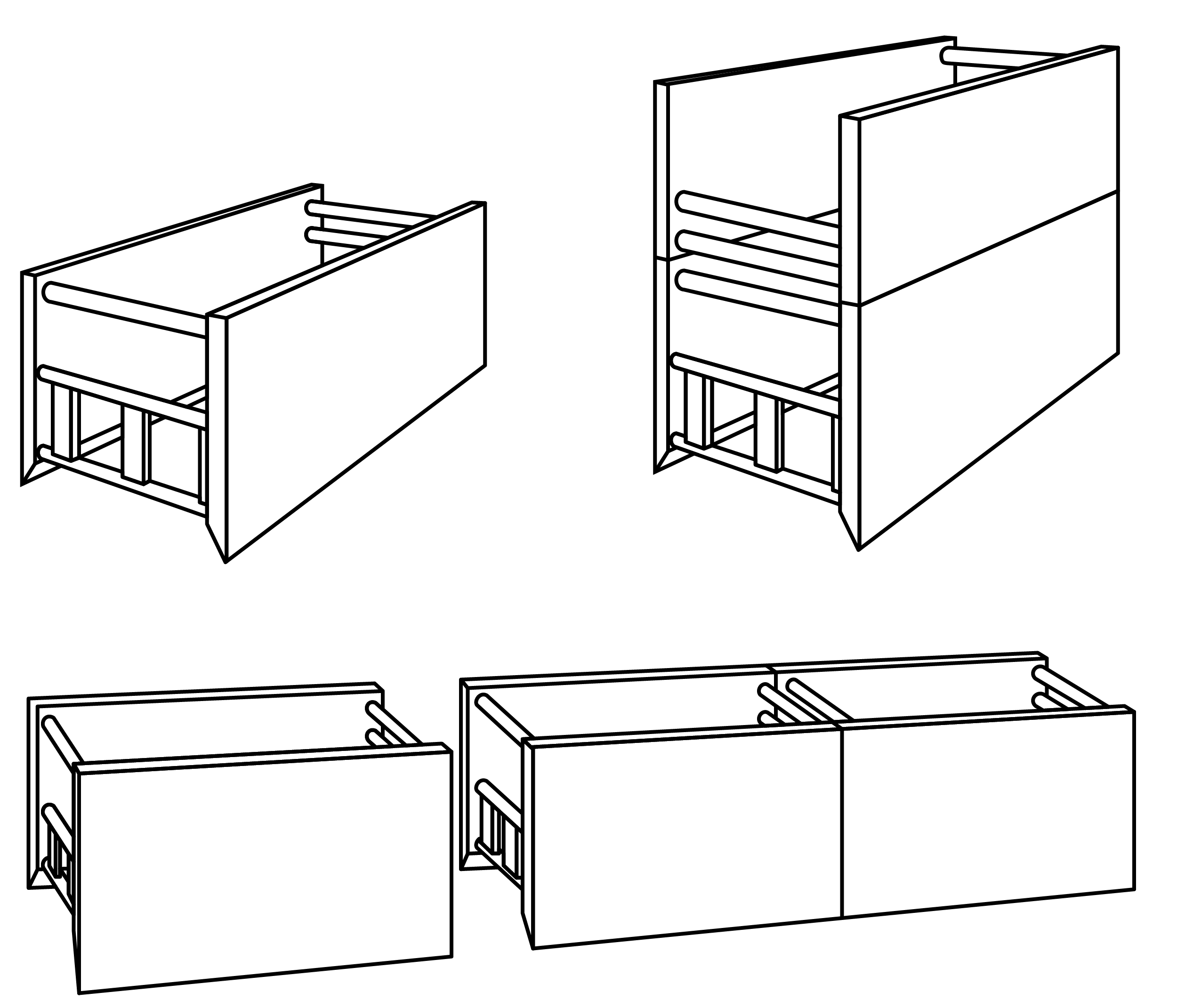
- Tabulated data
Use tabulated data such as tables and charts approved by a registered professional engineer to design the excavation. These data must be in writing and must include enough explanatory information, including criteria for making a selection and limits on use of the data, for the user to make a selection.
At least one copy of the data, including the identity of the registered professional engineer who approved it, must be kept at the worksite during construction of the protective system. After the system is completed, the data may be stored away from the jobsite, but a copy must be provided upon request to the Assistant Secretary of Labor for OSHA.
Protect adjacent structures
- Excavations below the base or footing of any foundation or retaining wall are not allowed unless certain criteria specified by OSHA are met.
- Materials and equipment must be correctly maintained because defects and damages can create excavation hazards.
The Occupational Safety and Health Administration (OSHA) standard requires an employer to provide support systems such as shoring, bracing, or underpinning to ensure that adjacent structures such as buildings, walls, sidewalks, or pavements remain stable. The standard also prohibits excavation below the base or footing of any foundation or retaining wall unless:
- A support system such as underpinning is present,
- The excavation is in stable rock, or
- A registered professional engineer determines that the structure is far enough away from the excavation and that excavation will not pose a hazard to employees.
Excavations under sidewalks and pavements are prohibited unless an appropriately designed support system or another effective means of support is provided.
Install and remove protective systems
The standard requires the following steps to be taken to protect employees when installing support systems:
- Connect members of support systems securely,
- Install support systems safely,
- Avoid overloading members of support systems, and
- Install other structural members to carry loads imposed on the support system when individual members need to be removed temporarily.
In addition, the standard permits excavation of two feet or less below the bottom of the members of a support or shield system of a trench if the system is designed to resist forces calculated for the trench’s full depth. In addition, there must be no indications, while the trench is open, of a possible cave-in beneath the support system. Also, coordinate installation of support systems closely with excavation work.
As soon as work is completed, backfill the excavation when dismantling the protective system. After the excavation is cleared, remove the protective system from the bottom up, taking care to release members slowly.
Maintain materials and equipment
An employer is responsible for maintaining materials and equipment used for protective systems. Defective and damaged materials and equipment can cause failure of a protective system and other excavation hazards.
To avoid possible failure of a protective system, ensure that:
- Materials and equipment are free from damage or defects,
- Manufactured materials and equipment are used and maintained consistent with the manufacturer’s recommendations to prevent employee exposure to hazards and while in operation, and
- A competent person examines any damaged materials and equipment. Unsafe materials and equipment must be removed from service until a registered professional engineer evaluates and approves them for use.
Understand additional hazards and protections
- Employers must address several precautionary measures to keep workers safe from falls, falling loads, and mobile equipment-related perils.
- Hazardous atmospheres or the possibility of them necessitate site testing done by a competent person, as well as controls and rescue equipment for employees.
In addition to the hazards covered in other sections, employees need to be aware of other dangers.
Falls, falling loads, and mobile equipment
Besides cave-ins and related hazards, workers involved in excavation work are exposed to dangers involving falls, falling loads, and mobile equipment. To protect employees from these hazards, the Occupational Safety and Health Administration (OSHA) requires an employer to take the following precautions:
- Keep materials or equipment that might fall or roll into an excavation at least two feet from the edge of excavations, or use retaining devices, or both.
- Provide warning systems such as mobile equipment, barricades, hand or mechanical signals, or stop logs to alert operators to the edge of an excavation. If possible, keep the grade away from the excavation.
- Provide scaling to remove loose rock or soil or install protective barricades and other equivalent protection to protect employees against falling rock, soil, or materials.
- Do not let employees work on faces of sloped or benched excavations at levels above other employees unless the employees at the lower levels have adequate protection from falling, rolling, or sliding material or equipment.
- Prohibit employees from standing or working under loads being handled by lifting or digging equipment. Require workers to stand away from vehicles being loaded or unloaded to keep them from being struck by any spillage or falling materials. Operators may be permitted to remain inside cabs of vehicles if those cabs supply adequate protection from falling loads during loading and unloading operations.
Water accumulation
Among additional hazards stemming from water in an excavation are undermining the sides and making it more difficult to get out of the excavation. The OSHA standard forbids employees to work without adequate protection in excavations where water has accumulated or is accumulating. Such precautions can include special support or shield systems to prevent cave-ins, water removal to control the water level, or the use of a safety harness and lifeline.
If water removal equipment is used to control or prevent water accumulation, an employer must ensure that a competent person monitors the equipment and its operation to ensure proper use. OSHA standards also require the use of diversion ditches, dikes, or other suitable means to prevent surface water from entering an excavation and to provide adequate drainage of the adjacent area. In addition, a competent person must inspect excavations subject to runoffs from heavy rains.
Hazardous atmospheres
A competent person must test any excavation deeper than four feet or where an oxygen deficiency or a hazardous atmosphere is present or could reasonably be expected, such as a landfill or where hazardous substances are stored nearby, before an employee enters it.
If there are any hazardous conditions, the employee must be supplied with controls such as proper respiratory protection or ventilation. In addition, when controls are used to reduce the level of atmospheric contaminants to acceptable levels, conduct testing as often as necessary to ensure the atmosphere remains safe.
If hazardous atmospheric conditions exist or may reasonably be expected to develop in an excavation, provide emergency rescue equipment such as a breathing apparatus, safety harness and line, and basket stretcher and be sure this gear is readily available. All such equipment must be attended when in use.
Note: In addition to the Excavation standard’s provisions on hazardous atmospheres in excavations, OSHA’s Confined Spaces in Construction standard (29 CFR Part 1926, Subpart AA) applies to non-excavation work within a confined space located in an excavation. These standards are intended to complement each other and address two distinct hazards: hazardous atmospheres in excavations and additional hazards associated with confined spaces located within excavations.
For example, the Confined Spaces in Construction standard covers entry into a prefabricated storm drain, other pipe, or manhole even if located at the bottom of an open excavation.
Performing certain types of work in an excavation, such as painting and welding, can expose employees to breathing dangers. In addition, equipment operating near the excavation can expose workers to breathing hazards including carbon monoxide, which bonds with human hemoglobin cells 50 times tighter than oxygen.
Oxygen can also be displaced by different gases and compounds in the trench and surrounding area. The proper level of oxygen required is approximately 21 percent (variable depending on elevation and other factors). A deficient atmosphere is less than or equal to 19.5percent oxygen, and an oxygen-enriched atmosphere is greater than or equal to 23.5% (which can cause fire and explosion). Oxygen can also be absorbed by oxidization of metal and chemical processes in a trench.
Protect employees
- Safe access and egress should be available for all employees working in trench excavations four feet or deeper.
- OSHA urges companies to have an emergency response procedure in place and rescue equipment ready for any accident.
There are certain things an employer can do to protect employees working in excavations:
- Provide means of access and egress,
- Supply protective equipment,
- Inspect the excavation and site, and
- Provide emergency response equipment.
Provide means of access and egress
The Occupational Safety and Health Administration (OSHA) requires an employer to provide safe access and egress for all excavations, including ladders, steps, ramps, or other safe means of exit for employees working in trench excavations four feet or deeper. These devices must be located in the excavation within 25 feet of all workers.
Any structural ramps used in an operation must be designed by a competent person if they are used for employee access or egress, or by a competent person qualified in structural design if they are used for vehicles. Also, structural members used for ramps or runways must be uniform in thickness and joined in a manner to prevent tripping or displacement.
Supply protective equipment
An employee who enters a bell-bottom pier hole or similar deep and confined footing excavation must wear a harness with a lifeline. The lifeline must be attached securely to the harness and must be separate from any line used to handle materials. Also, while the employee wearing the lifeline is in the excavation, an observer must be on hand to ensure that the lifeline is working properly and communication with the employee is maintained.
Inspect the excavation and site
The standard requires that a competent person inspect an excavation and the areas around it daily for possible cave-ins, failures of protective systems and equipment, hazardous atmospheres, or other dangerous conditions. Inspections also are required after natural events such as heavy rains or man-made events such as blasting that may increase the potential for hazards. If the inspector finds any unsafe conditions during an inspection, employees must be cleared from the hazardous area until safety precautions are taken.
Larger and more complex operations should have a full-time safety official who makes recommendations to improve implementation of a safety plan. In a smaller operation, the safety official may be part-time and usually will be a supervisor.
Supervisors are the contractor’s representatives on the job and should conduct inspections, investigate accidents, and anticipate hazards. They should ensure that employees receive on-the-job safety and health training. Supervisors also should review and strengthen overall safety and health precautions to guard against potential dangers, get the necessary worker cooperation in safety matters, and make frequent reports to the contractor.
Provide emergency response equipment
Emergency rescue equipment is required by OSHA when a hazardous atmosphere exists or may reasonably be expected to develop during excavation work.
However, the agency recommends that companies have emergency response procedures in place, and rescue equipment ready, in case any accident occurs. Ensure the procedure includes:
- Who will provide immediate jobsite rescue and aid;
- Who will notify the authorities and rescue personnel;
- Who will meet, advise, and direct rescue personnel; and
- What emergency response equipment will be available on the jobsite, where it will be kept, and who will be trained to use it.
If there is an accident at the excavation site, the time between when the accident happened and when rescue personnel arrive is critical. Any assistance that workers can give the victim, without endangering themselves, should be done immediately. Using heavy equipment in a rescue attempt of a trapped person should be avoided. Extreme caution should be taken in situations where serious injuries or death have occurred.