RMP vs. PSM: A Quick Guide to Chemical Safety Regulations
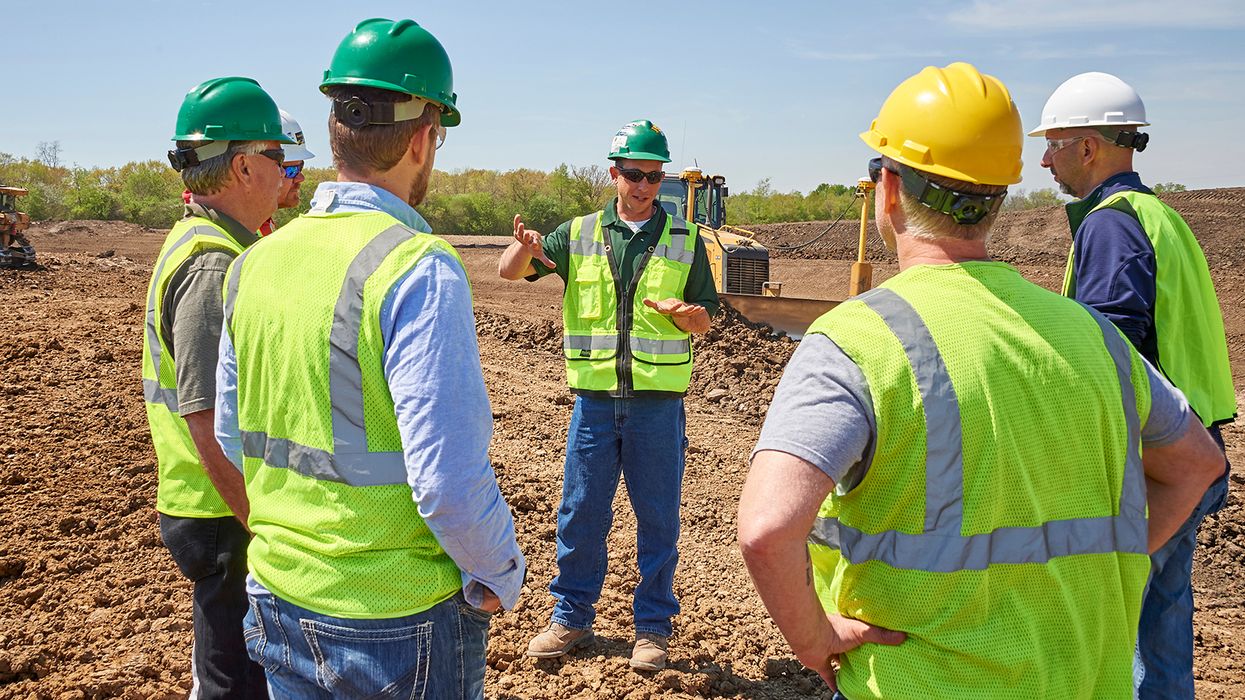
Do you play a role in developing safety plans under both OSHA’s Process Safety Management (PSM) standard and the EPA’s Risk Management Program (RMP)? This article provides a clear breakdown of the key differences between these two regulatory programs and what you need to know, even if your workplace is only subject to one. Understanding the distinctions can help ensure compliance and improve safety outcomes.
It’s vital for all employees who work with or around hazardous chemicals—whether stored, mixed, or processed—to understand the risks involved. They should be trained to recognize how each process functions and know how to detect when equipment is malfunctioning or operating outside of safe parameters.
Data from the Chemical Safety and Hazard Investigation Board (CSB) highlights the importance of vigilance: In fiscal year 2023, the number of reportable chemical incidents increased by 51% compared to the previous year. Incidents involving serious injuries increased by 11%, while fatal chemical accidents surged by 78%.
Employees must be equipped with knowledge about emergency response procedures and understand who to contact in the event of equipment failure, chemical release, or other emergencies.
Administered by the Occupational Safety and Health Administration (OSHA), PSM applies to processes involving specific quantities of hazardous chemicals listed in Appendix A of the PSM standard. It also covers flammable gases or liquids with low flashpoints, as well as specific activities such as the manufacture of explosives or pyrotechnics.
There are exceptions to the standard, including retail facilities, some on-site fuel use, storage in atmospheric tanks, oil or gas well operations, and remote, typically unoccupied sites. As of June 2024, OSHA is actively working on updates to the PSM standard through its ongoing rulemaking process.
The Environmental Protection Agency (EPA) enforces the Risk Management Program under 40 CFR Part 68. This rule is designed to prevent chemical accidents at facilities handling hazardous substances and requires detailed planning and coordination with local emergency response teams.
RMPs must include critical information to support fire, police, and emergency response planning. Public access to RMPs enhances transparency and promotes community preparedness.
Both PSM and RMP are mandated under the Clean Air Act, but they serve different primary purposes:
OSHA oversees PSM, while the EPA administers RMP. While both programs have similar requirements, RMPs also require submission to the EPA and local emergency responders to ensure they are informed of risks in the event of a release.
If your facility uses any chemical listed in the List of Regulated Substances (40 CFR 68.130) above a designated threshold, you are required to comply with the EPA’s RMP regulations. This includes developing a risk management program and submitting an RMP to the EPA. These plans must b e reviewed and resubmitted every five years to remain in compliance.
Facilities must report chemicals that are:
Many of these substances also appear in OSHA’s PSM Appendix A list of Highly Hazardous Chemicals, indicating potential regulatory overlap.
Both the RMP and PSM programs share a common goal: reducing the risk of chemical accidents through structured planning, training, and communication. However, their areas of focus—external vs. internal protection—differ.
Creating and maintaining either program requires:
Employers should determine if both standards apply to their operations and ensure all requirements are met to safeguard employees, the public, and the environment.
Under the Clean Air Act, RMPs protect the community, while PSM safeguards workers. Understanding your obligations, particularly when both programs apply, is essential for ensuring safety and regulatory compliance.