General workplace ventilation requirements
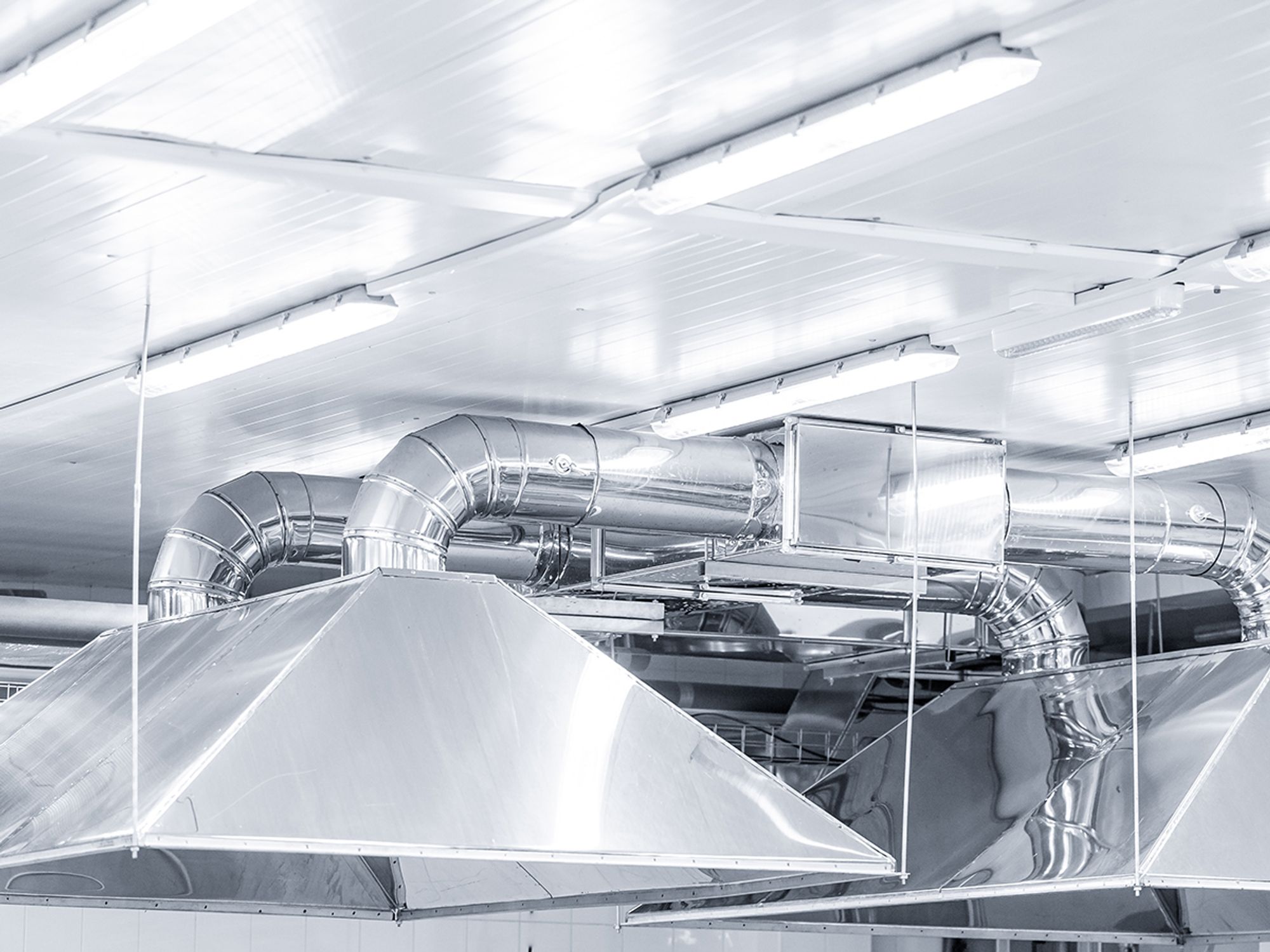
- Engineering control techniques such as isolation and substitution can reduce chemical exposure.
Perhaps the most widely used technique for controlling chemical exposure is the use of ventilation. General ventilation uses the movement of air within the general workspace to displace or dilute contaminants with fresh outside air.
However, general ventilation may not be the preferred control method due to the large volumes of air movement it requires. Local exhaust ventilation uses a much smaller volume of air and controls emissions at the point the contaminants are generated. Isolation and substitution controls should also be considered while creating a workplace or containment ventilation plan.
Isolation
Isolation involves placing a physical barrier between the hazardous operation and the worker. Many modern, automated manufacturing processes are fully enclosed in ventilated cabinets. The effectiveness of such a control technique depends on how frequently the workers have to enter the enclosure during normal operations.
In other situations, the worker, rather than the process or machine, can be placed in an enclosure having a controlled atmosphere. Many processes that involve potential chemical exposures are operated remotely by workers in air-conditioned booths isolated from the hazardous materials.
Substitution
Substitution refers to the replacement of a toxic chemical in a particular process or work area with a less toxic or non-toxic product. Properly applied, substitution can be a very effective control technique.
However, the proposed substitute must be carefully evaluated before use to ensure:
- That it performs in a similar manner to the product being replaced,
- That it doesn’t inadvertently introduce another hazard, and
- That it is compatible with existing manufacturing equipment and processes.
The success of these engineering control techniques will depend on the physical properties of the chemicals and emissions encountered (boiling point, vapor pressure, etc.) and the process operating conditions. In some cases, particularly with cleaning solvents, substitution may provide the quickest and most effective means of reducing exposure. In other situations, a major effort may be required to alter processes or install or expand local or general dilution ventilation.
According to the Occupational Safety & Health Administration (OSHA), engineering controls and improved work practices are able to reduce exposure levels to the required levels in almost all circumstances. However, respiratory protection may be necessary to complement engineering controls in some circumstances and to achieve compliance in specific operations in some industries.