Dockboards
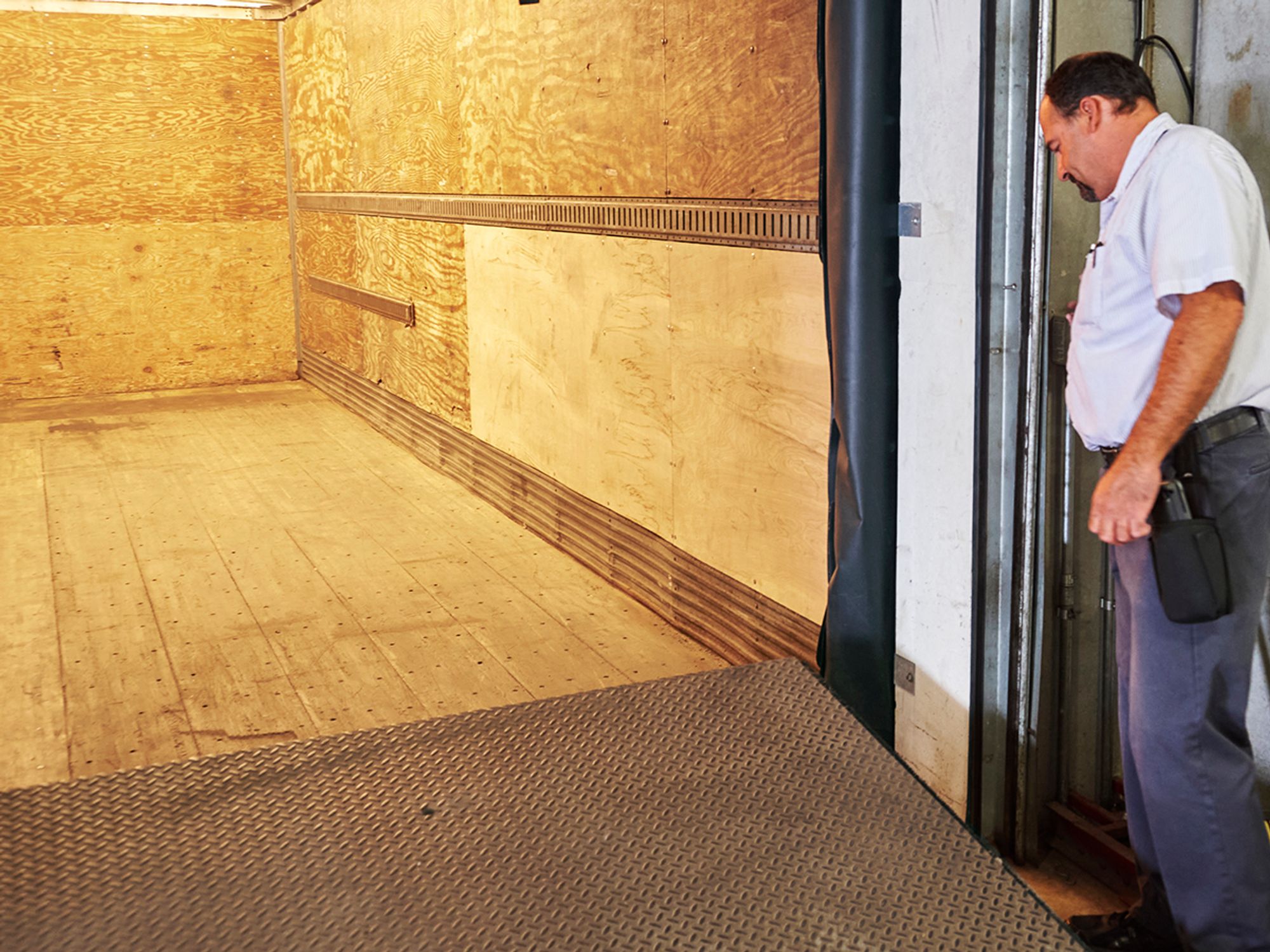
- Dockboards are considered walking-working surfaces and must comply with OSHA’s requirements.
A dockboard is any device used to span a gap or compensate for the difference in levels between a loading platform and a transport vehicle. Some examples include bridge plates, dock plates, and dock levelers. Dockboards can be permanent or portable.
All dockboards put into service after January 17, 2017, must comply with the requirements of the Occupational Safety and Health Administration (OSHA)’s Walking-Working Surfaces standard.
Dockboards are considered walking-working surfaces and employers must evaluate them for fall hazards. If a fall hazard exists, the employer must utilize some form of fall protection.
The evaluation also helps employers determine if their dockboards can support the maximum intended load. The maximum intended load (weight and force) includes all employees, equipment, vehicles, tools, materials, and other loads reasonably anticipated.
Employers must decide, based on the maximum intended load, what material should be used to construct a dockboard. For example, portable dockboards that only need to support lightweight loads moved by a hand truck could be made from aluminum. On the other hand, steel may be needed to construct a portable dockboard that will have to support the weight of a motorized pallet jack, load, and employee.
Dockboard training
OSHA considers a dockboard to be equipment and requires that employers train each employee before the initial use of a dockboard. The training must include proper placement and how to secure the dockboard to prevent movement.
Portable dockboards
Each employer must evaluate their needs and choose appropriate dockboards for the work that is being done.
Portable dockboards must be secured by either anchoring them in place, or using equipment or devices to prevent them from moving out of a safe position. If neither of the two are feasible, OSHA requires that the dockboard make sufficient contact in the transport vehicle. OSHA considers sufficient contact to be at least 4 inches inside the transport vehicle.
Portable dockboards must also have a means for safe handling. OSHA suggests handholds or other means of gripping the dockboard. When portable dockboards will be moved mechanically, OSHA suggests the use of forklift loops, lugs, or other effective means. The employer must evaluate how to safely move the portable dockboard and prevent employee injuries.